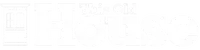
E18 | Westford Historic Renovation | Under a New Roof
Season 46 Episode 18 | 23m 42sVideo has Closed Captions
The Colonial Revival hip roof takes shape and the foundation is opened for a garage door.
Charlie and Tom Silva work in the attic, installing a hip beam and roof rafters to match the original roof. Downstairs, building scientist Joe Lstiburek discusses with Kevin O'Connor how insulating exterior walls can damage siding if energy flow isn't considered. Later, Mark McCullough brings in a stone cutter to cut through the original foundation, creating a garage door opening in the basement.
Problems with Closed Captions? Closed Captioning Feedback
Problems with Closed Captions? Closed Captioning Feedback
Funding for THIS OLD HOUSE is provided by The Home Depot and Renewal By Andersen.
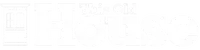
E18 | Westford Historic Renovation | Under a New Roof
Season 46 Episode 18 | 23m 42sVideo has Closed Captions
Charlie and Tom Silva work in the attic, installing a hip beam and roof rafters to match the original roof. Downstairs, building scientist Joe Lstiburek discusses with Kevin O'Connor how insulating exterior walls can damage siding if energy flow isn't considered. Later, Mark McCullough brings in a stone cutter to cut through the original foundation, creating a garage door opening in the basement.
Problems with Closed Captions? Closed Captioning Feedback
How to Watch This Old House
This Old House is available to stream on pbs.org and the free PBS App, available on iPhone, Apple TV, Android TV, Android smartphones, Amazon Fire TV, Amazon Fire Tablet, Roku, Samsung Smart TV, and Vizio.
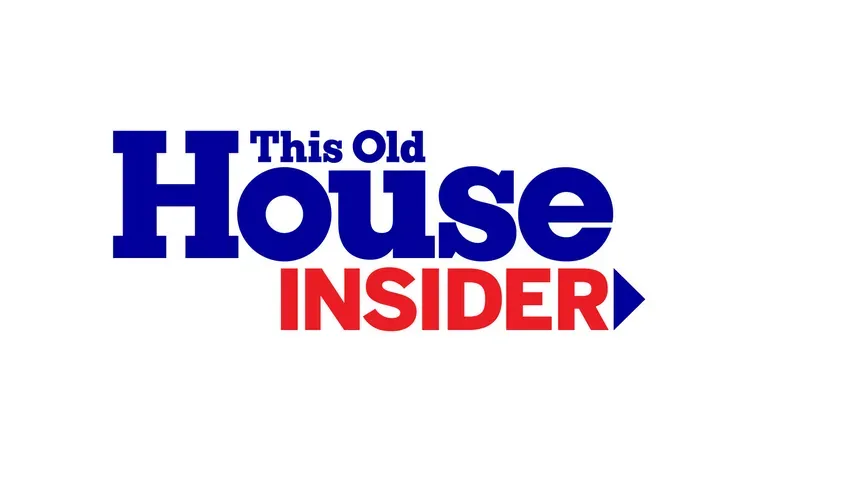
This Old House Insider Newsletter
Get This Old House exclusive stories, tips, and behind-the-scenes information delivered right to your inbox every month.Providing Support for PBS.org
Learn Moreabout PBS online sponsorshipKevin: Today... Charlie: Here in Westford, we're framing our hip roof and our big window walk.
Tom: That's good, because I like a big window walk over a "widdle" widow walk.
Charlie: Yeah.
[ Laughs ] Kevin: Then we'll learn how these old walls will get an upgrade courtesy of a building science pro.
Mark: And to give this house a garage, we're going to cut through this foundation.
♪♪ ♪♪ Man: Ahh.
That's it.
♪♪ ♪♪ Kevin: Hey, there.
I'm Kevin O'Connor.
And welcome back to "This Old House" and to our project here in Westford, Massachusetts, about 30 miles northwest of Boston, where we are working on this house right here.
It's got an interesting story.
Several years ago, it suffered a three-alarm fire which started in the back left corner, took off the entire roof, and most of the fire damage, fortunately, stopped there.
They were able to put a deck on it, cover it with rubber, and protect the inside.
Now, it sits right in the center of town, sort of an iconic house.
Built in 1893, and it's in the Colonial Revival style.
And our homeowners, they actually bought it years after the fire from the town, with the hopes of completely bringing it back to its former glory.
Come on inside and we'll show you some of the beautiful details.
Hey, Tim.
Tim: Hey, Kev.
Kevin: So in addition to the fire, we also had smoke and water damage inside.
That means we had to take all the plaster off, all the lath.
They were able to save some of the finer details, but you can see we're back to the studs.
The windows, which are double hung, are all coming out.
Most of them are out already.
We're going to put back in brand-new windows, triple-glaze, all throughout the house.
Here's one of those beautiful details right here -- fireplace -- you can see.
Tiles, millwork all still in place.
As you walk through here, come into what was kitchen/dining room, we've got some of the wainscot on there.
And then this area, this was a walkout bay window -- rotted out top and bottom.
So Charlie took that out, is going to have it repaired.
Come back in here, you can see there's some floor damage.
Again, though, check out the high ceilings.
And then right here -- Oh, yeah.
So there was a chimney.
Went through the roof, second floor, first floor, down into the basement.
Tommy and Charlie took this out, and I think -- Hey, Charlie.
Charlie: Hey, Kevin.
Kevin: He is down there doing some Work in the basement, so let's catch up with him.
[ Rattling ] Charlie!
Charlie: Kevin.
Kevin: We don't have another tunnel in our future, do we?
Charlie: Not a tunnel, but this is going to be conditioned space, believe it or not.
So this is forcing us to take this slab out.
Kevin: Wow.
So they want to, what, just turn it into extra space?
Charlie: Well, there's a garage over there.
There's going to be a -- We're going to put plumbing in for a future bathroom.
Kevin: Yeah.
Charlie: But back to our energy code, we have to insulate underneath this slab and the walls because it's going to be conditioned space.
Kevin: So you got to take all this concrete out?
Charlie: Eight inches below where we're standing now we're actually going to come down three inches of closed-cell insulation, and then we'll do a new pour.
Kevin: Right.
Okay.
Charlie: But this is where our chimney came down from above.
Kevin: I saw that.
Charlie: No footing.
Kevin: None.
Charlie: Which made me think about these brick columns and what's under here.
The engineer actually approved all of these brick columns the way they were structurally.
So one of the brick columns was right here, and I wanted to see what was under it, since all of this has to come out.
And this was our footing back in the day -- nice big flat rock.
Kevin: So if the engineer says what's here is okay, why are you upsizing?
I mean, I know we got a lot going on with the new roof and widow's walk and stuff.
Charlie: It's not really that we're upsizing.
We have to put new footings in 'cause all of this has to come down eight inches in total so we can spray closed-cell foam over it because it's conditioned space.
Kevin: Yeah.
Charlie: The energy code once again.
Kevin: How could you not put footings in once you're chopping everything up?
Charlie: That's right.
Kevin: And so just plumb for a future bathroom, get it set up, Just sort of future-proof?
Charlie: That's right.
And if it's in the budget, we'll put it in.
But at least the plumbing will be in.
Kevin: Okay, well, not a tunnel but a lot of industry.
Charlie: It's a lot of work.
Kevin: I'll let you get back to it.
Charlie: Alright.
Kevin: Thanks, Charlie.
♪♪ ♪♪ ♪♪ Charlie: Well, this is a section of the roof that you and I peeled that rubber back and exposed all those burned ceiling joists.
Tom: Yeah, they were gone.
Charlie: And so the more we pulled back, I decided to bring the engineer in.
He did a site visit, and he said all this has to come off and be reframed.
So we had a good stretch of weather and decided to do it in a matter of days.
And look where we are now.
Tom: Yeah, I mean, I'm not surprised the engineer wanted it replaced, because I actually feel better about that because now we have a nice flat, straight floor system that's structured correctly.
And they also put a new knee wall in, because that was gone when they took the roof off.
And right here there's going to be a new dormer that's going to be framed.
And in this dormer right here, it's going to rest on the widow's walk.
Now, what we're framing today is a hip.
Right here you have the two LVLs where the intersection of all the rafters come up and meet.
Alright, now we got to get the length for our outside hip beam right here.
Charlie's marking the top.
If you look right here, you can see we have them marked for the two beams right here.
We have an end transition where we're going to be on our seat cut.
This end transition has to end at the same termination of the common rafter.
Alright, so now we have the thickness of each hip beam.
Charlie is marking the top up there where it ends.
And I'm going to take my tape measure.
He's going to hold it on a line and he's got the same thing up there.
He's marked from the outside of the corner the thickness of the hip beam.
The top of the hip beam's going to line up with the common rafters.
I'm going to bring it down.
You got it?
Charlie: That's it right there.
Tom: 219 15/16.
Give that measurement to Tim.
219 15/16, Tim.
♪♪ ♪♪ Charlie: You good?
Tom: Yeah.
We're there.
Can you tack that?
Charlie: I'm right where I have to be now.
Tom: Alright.
Nails into the ridge.
Charlie: Ready?
We're good.
Tom: So now we have a string line right down the middle to make the beam straight.
Charlie: There you go.
Tom: Now, once we have them even and the beam is on the string line, Charlie can nail it.
So put a couple of tacks in that, Charlie.
Charlie: Right there.
Tom: We have to make sure the beam's straight, because if we nail it with the beam being crooked, it will stay crooked.
If we nail it with the beam on the line, it'll stay straight.
Okay, now we're going to push this over to line it up with the string.
Charlie: How's the top?
Tom: It's just -- Charlie: Good?
Tom: Good.
Alright, tack that brace to hold it in place.
Alright, good.
Alright, nail it up.
Alright, that's tacked.
It's straight.
Now we can start measuring for our rafters.
Alright, now we're going to find our positionings for each rafter.
Off of the same rafter, we're both going to measure.
That rafter has been made sure that it's running straight and true.
I'm going to take a measurement.
I'm going to mark 16 on center right here at the high point.
Come down, making sure that the tape is square off of the rafter.
Okay, so now that I have my long point for each one of the hip's rafters, I'm going to measure down at the seat cut right here on the wall and measure up to my point.
Give that measurement to Tim.
And that is...60 inches.
So that's 60 inches.
98 9/16.
Tim: Got it.
Tom: Charlie, take over.
Charlie: 117 9/16.
136 7/8.
Tim: Got it.
Thank you.
Tom: And once we get everything cut, we know it's going to fit.
We start putting the puzzle together, and believe it or not, it goes pretty quick.
♪♪ ♪♪ Alright, now we got to do the same thing on this side.
Got to find a rafter that's really straight and come off of that same rafter all the way up.
♪♪ Good?
♪♪ ♪♪ Alright, all the rafters are in, framed to the hip beam, and they're nice and even.
Charlie: Check out this view.
Tom: Yeah, this is great.
Great view.
Charlie: Nice.
Tom: Well, they're making good progress.
By the end of the day, they should have this dormer framed and the roof sheathed.
Charlie: They will.
Tom: Yep.
Looking good.
♪♪ ♪♪ Kevin: You may not know the name Joe Lstiburek, but chances are you have benefited from his work.
As one of our country's foremost building scientists, his research has done a lot to make our homes comfortable but also energy-efficient and durable.
Hey, Joe.
Nice to see you again.
Joe: Yeah, good to see you.
Kevin: So as a building scientist, I know that you are concerned with the entire home's envelope, so, you know, the roof, the floors, as well as the walls.
We're just talking walls today.
Is that okay?
Joe: I'm a wall guy.
Kevin: Perfect.
I love to hear it.
So, we're doing a retrofit, but we want to sort of understand what was here when the house was built in 1893.
So tell us what was going on back then.
Joe: On the inside, we had plaster and lath, no insulation, boards, tar paper, wood siding.
Kevin: Which you actually like.
You say it worked well... Joe: Yeah.
Kevin: ...and they were doing the right thing back then.
Joe: Yeah, because after fire and structure, we worry about water.
Kevin: Water's the enemy.
Joe: And it's okay if things get wet if they dry.
Wetting followed by drying, whoo-hoo.
The trouble is, is that drying requires an exchange of energy.
Kevin: So you make a lot of heat in here.
It wants to get outside.
So that dried -- Joe: That allowed things to dry if they got wet.
How did it get wet?
Well, it would get wet because of rain at the laps of the siding.
As the rain runs down the siding, surface tension draws it up between the clapboards.
This is called capillarity.
It's, you know, you take basically a paper towel with tiny pores, and it wicks water up.
Kevin: Yeah.
Joe: Well, tiny gap wicks water.
So water's always been coming in, but, man, the energy just dried that water out, and life was great.
So what did we do?
We were insanely brilliant and stopped the energy flow.
Kevin: So when you say stopped the energy flow, that's the adding of the insulation.
And we know, just because of some of the telltale signs, when we see these round holes through the sheathing, we know that at some point they blew in something like cellulose from the outside.
Joe: Absolutely.
And because it was a spectacular insulation, what did we change?
Kevin: We stopped the energy flow.
Joe: The energy flow.
And so when things get wet and stay wet, bad stuff happens.
And the first thing that people noticed was the paint fall off their siding.
The wood expands and contracts, and the expanding and contracting stresses the paint, and the paint fails because it can't stretch.
So it's not pushing it.
It's expanding and contracting and pops off.
Kevin: Okay.
This is -- Wow.
That's a big mock-up there.
This is what we're thinking of doing with the existing house.
So that's the existing sheathing.
This is the existing two-bys.
But then we've added some items.
Joe: Yeah, we've added some -- to get some thickness, additional thermal insulation in the cavity.
You're using a very high performance cavity insulation, closed cell, two-pound density spray foam, and you're installing it correctly.
I have a smile on my face.
You're actually picture-framing it so that when the chemical reaction happens, it doesn't peel off the sides.
Kevin: So do it in two sprays, one spray, then fill it in with the second.
Joe: Exactly.
But guess what.
That would destroy the paint issue.
Except what do you got?
Kevin: Let's turn this around.
When you say that would destroy the paint, why wouldn't something that controls air, temperature, and vapor still cause a problem with the paint?
Joe: Well, because the water's coming from the outside.
Remember?
Kevin: It's getting behind the shingles from the outside.
Joe: Yeah.
But guess what.
This provides back ventilation and drainage for our cladding.
It's a high-tech wedgie.
It's a spectacular way of dealing with water that gets wicked between the laps of siding.
So you're going to have water drainage and air flow.
Kevin: So that allows drying.
Joe: Whoa!
You're a building scientist.
Kevin: Not quite.
And we've got one other layer on this which we are doing on this building.
So on the outside of the sheathing, Charlie is putting the new sheathing with the rigid foam insulation affixed.
Joe: Yay!
Whoo!
Kevin: Why do you love that?
Joe: Well, because I grew up in a cold place.
When it got cold, we would pull the sweater over the outside of us.
This insulation is a sweater for the outside of your building.
Magnificent.
Kevin: Well, this is good because we've got a stretch energy code to meet right here.
We've also got homeowners who are very energy-conscious.
So they've asked us to take it as far as we can.
You approve of this situation and all these layers?
Joe: If I had a house, I would do this.
Kevin: Okay.
We could do it because of the fire.
Everything on the inside was stripped, that plaster and lath, and everything on the outside is coming off.
Joe: Yeah.
Kevin: That's not practical for a lot of people who want to do a retrofit.
So if I couldn't do all of these, what do you recommend the regular folk do?
Joe: Well, you could strip the stuff off the inside and use spray foam.
Kevin: Mm-hmm.
Or cellulose?
Joe: Okay, now, the moment you do this, you're going to destroy the paint issue.
Kevin: Just like when we added cellulose to this house back in the '80s.
Joe: Exactly.
So how do you handle that?
Well, I never travel anywhere without wedgies.
Kevin: [ Laughs ] Can I see one of those?
And what do we do with these?
Joe: We use these to create a gap between the siding to prevent the water rising.
But you just drive them in beside each nail to create a small gap to prevent capillarity.
And the siding dries.
Kevin: So that breaks the -- this clap from touching that clap.
Doesn't wick the water.
Does it let air in?
Joe: Absolutely provides air.
It does everything.
It's awesome.
How do we know?
Well, we messed up thousands of buildings in the 1980s.
We blew them filled with cellulose, and the paint fell off, and we fixed it by putting in wedgies.
And so now we have the ability to retrofit buildings without causing a paint failure.
Kevin: Nice.
Joe: We just didn't know it in the '80s.
Kevin: Right.
Okay.
Well, I know that we have just sort of touched the tip of the iceberg here, but good information all the same.
Thank you, Joe.
Joe: A pleasure.
Kevin: Always a pleasure.
♪♪ Hey, Mark.
How you doing?
Mark: Kevin.
Kevin: What do we got going on back here?
Mark: Alright, so we're putting a garage in the basement now.
Kevin: I remember that, right.
Mark: So we have to make a nice clean cut.
We have our friend here, Ben, who's going to make a clean cut.
As you can see, he's got his brackets in place.
The brackets grab the rail.
The rail grabs the saw.
The saw grabs the blade.
Kevin: What's the matter?
You don't have a bigger blade?
Mark: We don't have a bigger blade, I know.
Kevin: Holy smokes.
Mark: So this blade you're looking at is a 32-inch blade all the way across.
Behind that is a 42-inch blade.
Ben starts with the smaller one and then continues on with the bigger one.
Kevin: And how thick is our wall?
Mark: So we have a 17-inch-thick wall.
Kevin: Wow.
Mark: Right.
We have granite on the outside, as you can see, but we have a mix of rubble on the inside.
You might be able to look through that window and check that out.
Kevin: I saw the rubble stone from the inside.
I didn't even think about that.
Mark: That's right.
Kevin: So the last time we worked with Ben, if I recall, we were cutting through concrete foundations.
Mark: Right.
Kevin: So a monolithic pour.
Mark: Yes.
Kevin: Everything stays together.
With individual pieces like this, mortar and all that, like, what are we expecting here?
Is this whole thing going to fall apart?
Mark: So there's going to be a lot of handwork involved.
And again, we're just going to take it as it comes to us.
So if we see a piece that's loose, we're going to grab it.
If we have an opportunity to push something into the hole, we'll take advantage of it.
Kevin: Alright.
Let's see what we get into.
Mark: Alright.
Let's go.
♪♪ ♪♪ Kevin, the key component that is being used by Ben right now is the water.
The water loosens up that blade and protects the diamond edges that are on the blade.
So very important.
Kevin: Well, the diamond edges have obviously done the trick.
That thing just cranked through that granite.
Mark: Yeah.
So I think Ben is pretty happy right now, because that was the tough point was going through that granite.
Again, I'm not really worried about the rubble, but if he gets through that easily enough, it's going to be a quick cut.
You can see the reason for the two blades.
The 32-inch blade, you can see that it's cut in half with the guide.
So that's why you need the 42 to poke through.
Kevin: Right.
Yeah.
Made short work of it, huh?
Mark: So I think this went a lot better than Ben may have thought.
But look at how clean that cut is.
That's great.
Kevin: That cuts so clean.
I'm thinking of places I could put a garage door in.
Cut through something in my house.
Mark: Yeah.
Everything stayed together on the inside, so... Kevin: That's nice.
Let's hope we get as lucky with the second one.
Mark: I think we will.
♪♪ ♪♪ ♪♪ ♪♪ Alright, Kevin, due to the roundness of that blade, it bellies out.
So on the inside, it's going to leave the cut about a foot and a half up off the ground.
Kevin: Right.
Mark: So Ben has a bunch of tricks in his bag.
He's going to pull one, which is actually going to be a chainsaw.
Kevin: Yeah.
Mark: And that's gonna clean up that cut that we have on the inside to do.
Kevin: Alright.
Alright, Mark, what's the plan of attack?
-Alright, Kevin, so we're going to start from the top, but we're going to want to try to peel back this veneer.
This is the original Chelmsford Westford granite -- historical.
They want us to save it, which we love.
So we're going to take it, put it on a pallet, and at a later date we're going to repurpose it.
Kevin: Get in on some of this mortar right here, see what we got.
Mark: Yep.
Charlie: Hey, Kev, you want to give me a hand?
Kevin: Yeah.
♪♪ ♪♪ Mark: Here you go, Kev.
Oh, this is great stone.
Kevin: You like it?
Mark: I love it.
♪♪ ♪♪ Yeah, just give that a flick.
♪♪ Ah, great.
Kevin: Charlie made short work of cleaning this up for us.
Mark: Oh, he did a great job.
Great job.
Kevin: And I love this cut.
I mean, that is so smooth.
Mark: It's so smooth, Kevin.
But it did leave us with a little problem.
You can see the rough face out on the outside.
Kevin: Oh, no.
Too smooth?
Mark: Too smooth.
So in the old days, I used to take my carbide hammer.
Kevin: Little waffle head right there would get you what you need.
Mark: That's right.
Unfortunately, I don't trust this build right here, so it's a little jiggly.
So I have another idea.
And that is a torch.
Kevin: Oh, yeah.
Mark: And all we do is we light up the torch.
We'll hold it back about two inches, and I'll just ride the stone up and down like that.
Face will pop.
Kevin: No kidding.
Mark: The rough will match the rough.
Kevin: Alright.
Can I inspect, Mark?
Mark: You sure can.
Look at that.
Kevin: Ooh, hot.
Mark: Yeah, yeah.
Kevin: But that's awesome.
I mean, that looks like the front right there.
Mark: Exactly.
Charlie: Looks nice.
Mark: Thanks, Charlie.
Kevin: So what else to finish it up?
Mark: So, as you can see, I have to plug in a few pieces of granite up top.
I'm going to redo these joints.
Take my brick hammer and I'm going to hit that edge just like that.
And it's going to soften the edge.
Kevin: Beautiful, love it.
Mark: And just make a better blend, right.
Kevin: Love that we can, you know, dress this up, work with the old granite, and save what we took out, too.
Mark: Yeah.
Charlie: Oh, yeah.
Kevin: Good progress, Charlie.
So what about next time?
Charlie: Well, now that we're weathertight, we got the sub starting HVAC, ductwork, and Heath is even doing the electrical layout.
Kevin: Love to hear it.
Alright, all of that next time.
So until then, I'm Kevin O'Connor.
Mark: I'm Mark McCullough.
Charlie: And I'm Charlie Silva.
Kevin: For "This Old House" here in Westford.
Kevin: Next time on "This Old House"... Our homeowners decided not to go with a traditional asphalt roof.
We'll show you what they decided on and how to install it.
And this attic space.
It's pretty cool.
-Hey, Richard.
-Richard: Hey.
How are you?
Kevin: All right.
You got the crew up here working hard.
Richard: We are well underway.
We're going to put a new heating and cooling system into this building, obviously.
Tom: Then we're going to light this on fire to see how flames and smoke travel through a balloon frame structure.
Kevin: That's next time.
Funding for THIS OLD HOUSE is provided by The Home Depot and Renewal By Andersen.